Highlights
Oxygen sensor wins R&D 100 Award
Text extracted from archived Argonne News Release (Jul. 8, 2005)
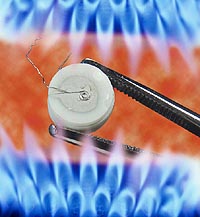
COMBUSTION MONITOR – This inexpensive, compact oxygen sensor developed by Ohio State University and Argonne monitors combustion processes ranging from internal combustion engines to coal-fired power plants. Argonne researchers provided the unique deformation bonding method for producing the sensor’s gas-tight seal.
ARGONNE, Ill. (July 8, 2005) — Argonne's research accomplishments have won four of the prestigious R&D 100 Awards, given to the world's top 100 scientific and technological innovations. One of the four Argonne winners winners is the "High-temperature potentiometric oxygen sensor", developed jointly with Ohio State University.
Oxygen sensor
Researchers at Argonne and at Ohio State have developed a compact sensor to monitor combustion processes in coal-fire power plants, petrochemical plants, blast furnaces, glass processing equipment, and even inside internal combustion engines. The high-temperature potentiometer oxygen sensor can withstand the heat inside the combustion chambers, allowing monitoring at the source in real time.
Developers include Jules Routbort and Dileep Singh, both of Argonne's Energy Technology Division (now Nuclear Engineering Division).
The new sensor is the first that does not require an external supply of reference air. Instead, the sensor is enabled by an internal reference air chamber, sealed by a unique deformation bonding method that joins the protective ceramic housing components together without altering the ceramic's oxygen conductivity. By eliminating the need for costly and bulky high-temperature external plumbing for reference air, this novel sensor provides unsurpassed oxygen-sensing accuracy for a cost that is approximately one-twentieth that of conventional oxygen sensors.
The information provided by the sensor is important to manufacturers, because it helps them be more energy-efficient and economical in their operations by achieving energy savings by optimizing the air-to-fuel ratio and the fuel oil viscosity. While various sensors have been available, industry has never before had a truly inexpensive means of accurately monitoring its boiler efficiencies to achieve the highest possible energy savings.
The new oxygen sensor overcomes the limitation of conventional oxygen sensors by having the capability to withstand temperatures up to 1600 degrees C and by allowing the engineering of small sensors – smaller than a dime – since no external air source or plumbing is required. The ceramic housing components of the sensor are joined without intermediate bonding materials through a unique deformation bonding method developed by the researchers. And the low cost of the sensor – about $200 – allows the use of multiple sensors, making it practical and affordable to monitor the combustion of oxygen and other materials throughout the combustion process.
The oxygen sensor development was sponsored by DOE's Office of FreedomCar and Vehicles Technology.
[ More News ]
Last Modified: Wed, April 20, 2016 9:33 AM